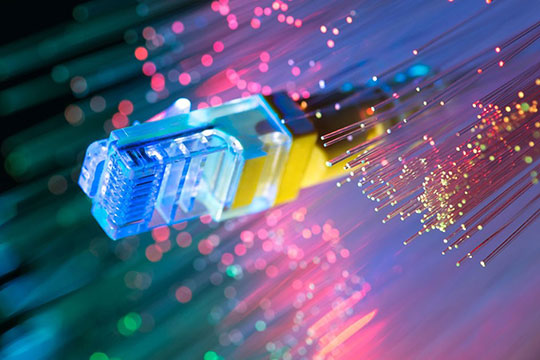
已经推出的机械MT切割技术,以及市场上已有的激光切割技术选项,我们应该将它们彼此对比一下。在这些系统问世之前,业界一直在使用手动划线器或某些专有解决方案来去除多余的光纤。下一步是手动打磨/去毛刺,以去除尖锐的边缘,然后将环氧树脂擦掉。使用MT端接时,甚至需要更多的手动过程才能去除多余的光纤。
除了需要提高产量和性能的半自动化工艺作业外,最近几年的产量增加还要求降低生产成本,因此,在高价值的MT端接组装工艺中,重点是高成本。
2006年推出了第一代激光切割刀,并创建了一个平台来处理裸光纤(单光纤和带状光纤),单插芯(单光纤和多模光纤以及大芯220 / 1000nm光纤)和多光纤插芯(MT)。在套圈尖端上方60-200um用单束CO2激光束以大约20摄氏度的速度劈开。
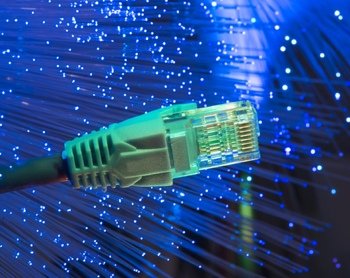
激光切割刀可以减少研磨薄膜,是对还是错
最新一代的单光纤劈裂来自Comet SSP。它使用双向激光束,可在插芯尖端上方30-35um处进行超低剖面切割,从而重新塑形光纤并去除几乎所有的环氧树脂。选择光纤连接器,当使用稳定的高质量抛光机时,该激光切割刀可使切割后的连接器直接进入单个最终抛光步骤。但是,在生产中,我们发现需要3um的碳化硅“半”步骤,以帮助在最后一步之前清洁密封垫圈。这意味着省去了所有金刚石膜抛光步骤,从而将大大降低抛光材料的成本,同时还提高了产能和产量。
SMA连接器应用
激光切割机还显示出对于大芯光纤应用(SMA连接器终止)具有明显的工艺优势,因为激光束切割可以无划痕的切割的较粗光纤。
SMA连接器大功率应用
对于高功率连接,在使用无环氧的独立式SMA的情况下,大多数公司在SMA连接器中使用诸如CrystalBond之类的支撑蜡来防止光纤在抛光过程中断裂,而之后需要将其拆除,这是一项费时的昂贵操作。使用激光切割操作消除了使用支撑蜡的需要,因为光纤很少从SMA尖端突出,因此在使用高稳定性抛光机时,可以直接进行抛光操作。同时减少了研磨膜的消耗。
束状光纤应用
注意到使用激光切割刀的巨大优势的另一个应用是光纤束。由于多根大光纤和大量的环氧树脂迫使手动劈开远离插芯尖端,因此激光劈刀将在一次操作中从多个方向“切割”多余的光纤,并为自动抛光提供平坦的光洁度。
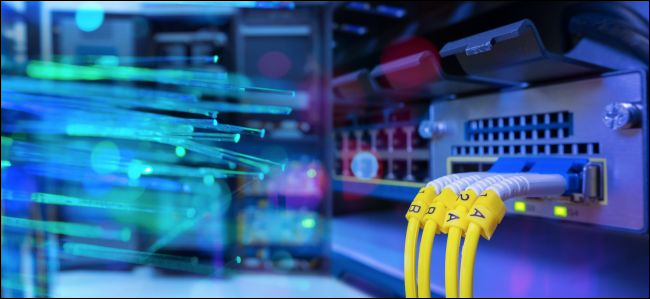
带状光缆的应用
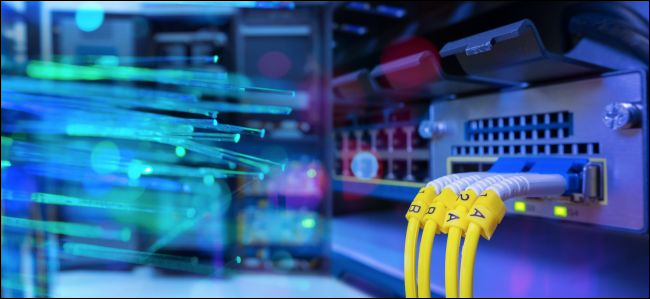
带状光缆的应用
对于带状光纤技术(例如MT套圈),激光切割刀可提供良好的均匀扫描,从而在所有光纤上提供均匀的光纤高度。传统的手动操作通常会显示出环氧刻痕上方的圆顶划痕或带有锐利光纤的笔直划痕。在抛光之前,最好对光纤进行仔细的手动去成核,以免光纤断裂进入环氧区域。
带状光纤切割的另一个优点是,可以消除环氧树脂的拍打,但可以保留和保护所有光纤。环氧平台产生更大的表面,使外部光纤上潜在的光纤断裂最小化,并且在抛光后还显示出更均匀的光纤突出,用干涉仪测量光纤的高度差。
激光与机械切割
要管理一种精确的材料以用大量的环氧树脂切穿光纤,并重复进行100.000的劈开,这是一个挑战。随着Phenix FO的Fibersect的推出,我们了解到它的切割非常一致,并且具有非常低调的切割重复性。距插芯尖端约70um的某个位置,低于标准的激光切割刀,但不是Comet-Ssp。光纤被完全包埋并在初始抛光阶段得到保护。尽管光纤表面比激光切割轮廓要粗糙得多,但这似乎不是缺点,因为需要进行抛光。相对于激光切割系统,较低的成本是另一个优势。
激光切割适合每个组装操作吗
切割系统的投资仍然很大,半自动化的过程看起来很有吸引力,但是财务数字需要反映出这些改进。手动切割操作和激光切割操作之间的初始比较通常集中在切割时间上。由于手动切割的操作时间仅需几秒钟,因此手动切割操作本身具有优势。尽管此操作的能力通常不是工艺瓶颈,但很明显,当考虑到减少单根光纤的抛光成本时,激光切割刀具有低切割效果的优势。通常,每月超过200.000-300.000终端的数量(取决于终端的类型)开始显示出考虑这种自动化类型的突破。
进一步研究脱核,去除环氧和相关的返工(由于抛光前的不一致)等过程,使比较变得有趣。嘉富光通信在全球范围内安装了超过10年的激光切割刀,可能是与您联系了解光纤组装操作所能带来的好处以及成本和质量的最佳途径。