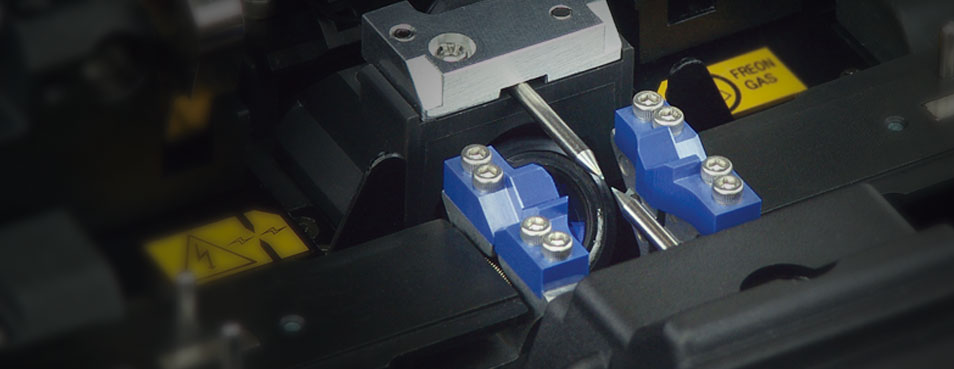
在整个大多数电信行业中,制造自动化蓬勃发展。这只是自动化成功的一个例子:融合拼接。操作员准备光纤末端,将其放入熔接机,然后按下按钮。设备测量并对齐末端,检查开裂,并执行接头测试以检查质量-完全无需动手。这种自动融合过程可节省更多成本并提高质量。
但是,让我们坦率地说一下典型的连接过程。我们认识到过去40年来的逐步改进,包括体积的增加(从一次抛光少数几个连接器到72个),以及自动化(从手压技术到批量抛光机)。也就是说,除了非常大规模的制造之外,当前的过程看起来非常相似。我们仍然手动组装连接器并手动处理它们。为了降低制造成本,我们的行业已将手工生产的光纤组件主要转移到了世界上劳动力成本较低的地区。
那么下一步是什么?大中型独立光纤装配厂如何在提高连接器质量的同时继续减少开支?我们的行业能否开发出“准备自动化”的工具和设备,这些工具和设备可以利用现有的通用自动化流程和软件,但仍提供光纤连接器装配空间所需的快速变化和灵活性?
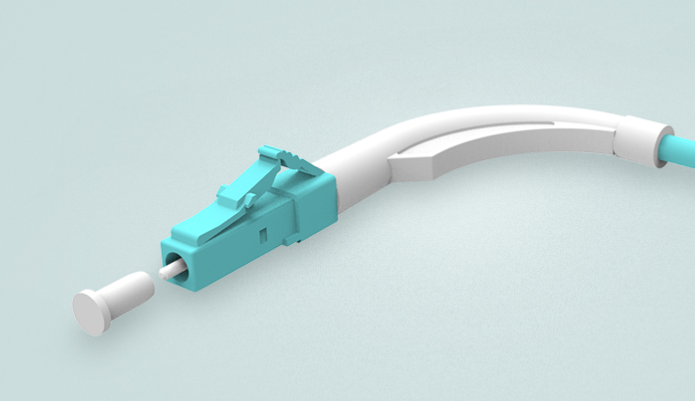
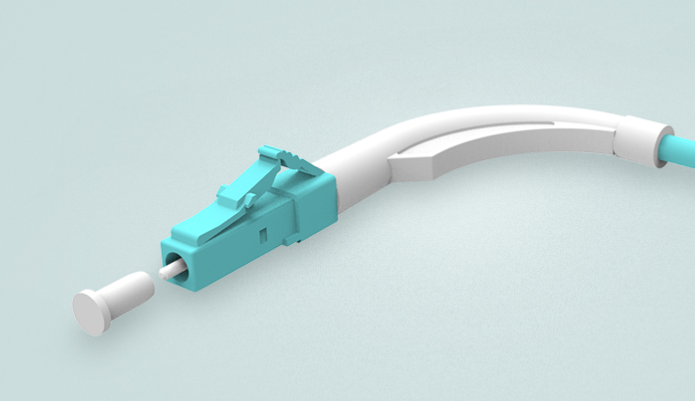
作为一个行业,我们必须团结一致,共同解决光纤连接的自动化问题。实际上,我认为自动化是光纤组装行业必不可少的下一步。但是,我们面临多重挑战。以下各段讨论了其中的一些挑战,然后提出了我提出的解决方案,这是我们行业克服障碍并向前迈出一大步的一种方式。
挑战:稳定的技术
光纤行业自动化的关注点之一就是您需要一种稳定的技术。同样,融合拼接是一个很好的例子:当公司开始使用融合拼接(与其他永久终止方法相对)时,过程变得非常稳定。无论是工厂拼接还是现场拼接,它们都使用相同的设备和稳定性。关键是,尽管开发了一种工艺(熔接),但工艺设备继续升级并增加了更多功能,但核心工艺并未改变。我们有一个过程,最初对操作员非常敏感,由于通用机器人技术和制造自动化技术的进步,该过程允许自动化。来自不同行业的一个例子是汽车的组装。几十年来,汽车制造商一直将机器人焊接在一起。
我们不能停止进步,而且我们也不想这样做,这意味着任何行业都无法幸免技术变化。(将福特的T型汽车与自动驾驶的特斯拉进行比较。)当我们看一下连接器和连接性的历史时,“进步”意味着不断开发和改进各种样式和类型的连接器,以降低成本,提高质量和易于组装。光纤组件最初使用的是适配的铜同轴光纤连接器(SMA光纤连接器),然后使用陶瓷套圈,非光纤断开器,然后使用具有许多不同样式和类型(LC,SC,FC,ST,MTR,MTP等)的多芯光纤连接器。 。然后,我们又从原来仅由工厂安装的连接器开始,再增加了可现场安装的连接器。
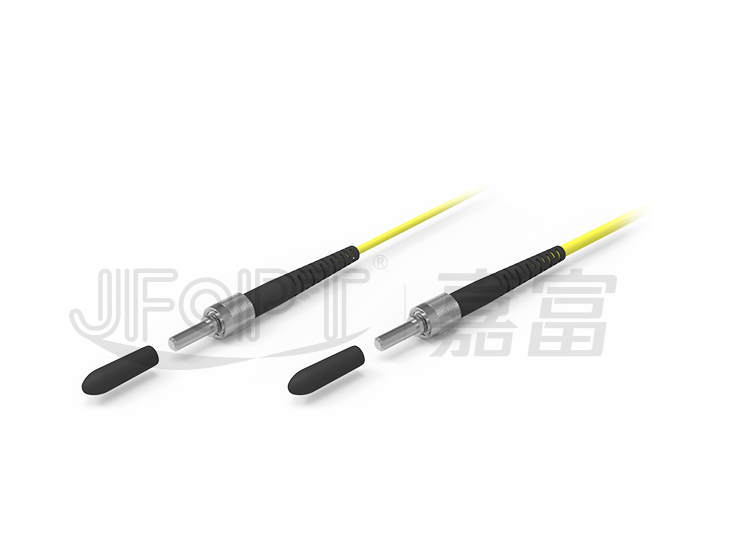
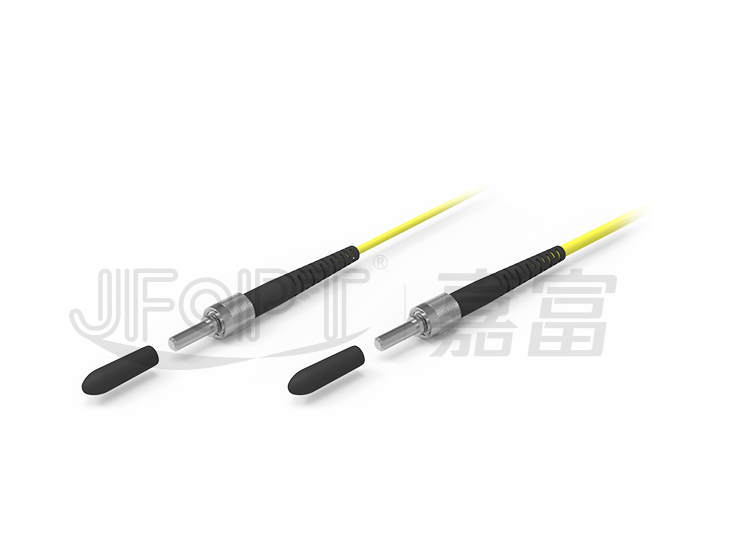
所有这些变体一起代表了一种不断改进的技术-有时是破坏性的技术。因此,当我们谈论自动化连接过程时,我们首先必须考虑自动化工厂组装的大量生产的连接器。(顺便说一句,我可以肯定地说,一些大型制造商已经通过高度专有的程序来自动化处理特定类型的大容量连接器。)
挑战:自动化的灵活性
注意:所有特定类型的连接器都必须符合称为焦点文件的可插拔性标准。本文档定义了允许不同制造商的产品相互配合的机械标准。RJ 45以太网铜连接器与此类似。因此,每个制造商都可以而且确实有不同的内部设计和创新。除此之外,我们实际上有数百个光纤和分支端可与这些连接器配合,您会发现在这种情况下需要非常灵活的制造过程。
此外,自动化的灵活性至关重要,因为我们不想扼杀未来的技术进步。每年,我们都会看到连接器方面的新创新。例如,存在许多所谓的无套圈连接器的变体。其他类型的连接器具有金属,陶瓷或模制塑料套圈。另外,某些连接器实际上通过凝胶提供了裸光纤到裸光纤的接口。这些变体中的许多已经出现或消失,或者发现了特定的壁ni。
我们的行业尚未实现连接器生产自动化的两个主要原因:
我们已经能够降低制造基本连接器主体的成本。其中大部分与自动注塑工艺和陶瓷套圈标准化有关。
通过将大型连接器操作转移到劳动力成本较低的地区,我们已经能够降低人工成本。这种迁移实际上已经阻碍了中型和大型,灵活的自动化市场,该市场可以应对连接器技术的快速变化。
有趣的是,我们的行业已经接受并要求复杂的测试和检查过程,并将其带入了非常高的自动化水平。我的意思是,该设备在其自己的环境中提供过程自动化测试,但不能与其他类似设备保持中立的接口。我们还没有将实际的连接器组装操作带到那种自动化水平。在该测试阶段,光纤装配厂仍在努力应对瓶颈,并迫切期望改进。
挑战:提高成本节约和质量
为了将自动化的连接转移到许多制造商,必须要有一个理由。原因是:随着我们的前进,每个连接器必须提供更低的损耗和更高的可靠性。连接过程必须生产出质量水平不断提高且成本降低的光纤组件。
如上所述,一个主要的挑战是处理这么多不同的连接器设计和材料。更重要的是,在不久的将来如何设计连接器?我们不想扼杀创新,同时降低成本并创造更高的可靠性。
但是,我们需要面对这样一个事实,即当今的组装过程在绝大多数公司中基本上都是非常手工的过程,而这种手工过程存在着严重的局限性。一位同事喜欢说:“人是两个西格玛。无论您做什么,您的可靠性和质量通常都达到2σ的性能。” 但是,我们需要提升到3西格玛甚至6西格玛的性能。为什么?因为在某些应用中,更高的性能绝对至关重要。例如,生命/安全问题,例如飞机上的飞行关键连接器,激光手术应用中的连接器以及911紧急或军事通信网络中使用的连接器。
Sigma的定义:
Sigma是有关统计意义的度量单位;用小写希腊字母sigma(σ)表示的标准偏差。它是给定数据集中的可变性量,而与数据点之间的紧密程度或分散程度无关。
正态分布是实验的结果,当绘制在图形上时,将在中间产生最高的形状,并在每一边逐渐变细。这通常称为钟形曲线。
偏差是给定数据点与平均值的距离。
标准偏差是所有平方偏差的平均值的平方根。
68–95–99.7规则是一种简写形式,用于记住位于正态分布均值范围内的值的百分比,正态分布的宽度为两个,四个和六个标准偏差。
在该正态分布曲线的平均值上方或下方绘制一个标准偏差或一个sigma,将定义一个区域,其中包括所有数据点的68%。上方或下方的两个Sigma将包含大约95%的数据,三个Sigma将包含99.7%的数据。
五Sigma的结果被认为是黄金标准,相当于发现结果是随机变化的结果的一百万分之一。六Sigma被认为是五分之一的结果随机的机会。从此术语衍生出著名的业务战略“六个Sigma”,它基于强制严格的质量控制程序以减少浪费。
为了进入光纤连接的工厂自动化的新高度,我们需要考虑柔性自动化的孤岛,这与电子行业的制造商采用柔性自动化的方式非常相似。考虑一下印刷电路板组装业务不断增长的复杂性。该行业从基本的印刷电路板到多层电路板,再到表面贴装技术。现在他们正在开发芯片对芯片技术。每一步,为上一代技术设计的设备都变得过剩,旧工艺迁移到了劳动力成本较低的领域。最终,每个技术流程都过时了-有时不到5年。
所以这里的问题是:
我们如何才能同时拥抱自动化而不扼杀新技术?
我们如何应对不断变化的要求和规格?
我们如何在短时间内实现自动化并为此付费?
一些自动化技术可以作为指导。例如,5轴和6轴机械臂的设计和制造非常灵活(从字面上看),因此多年来可以轻松对其进行更新。几个行业为自动化接口采用了标准化的软件模型,因此不同的制造商组件可以无缝地协同工作。可以说,这是一项保险政策,因此该技术不会很快过时。
为了应对光纤组装行业不断增长的成本要求,我们必须与组装设备制造商合作,共同商讨与软件和硬件相关的自动化过程接口。
实际上,我相信最终客户将推动对提高质量和装配灵活性的需求。对三西格玛到六西格玛性能的不断增长的需求将迫使光纤装配厂摆脱“质量测试”的工作方式,转向“质量内置”的方法。
在连接自动化方面,我们的行业正处于转折点。
在光纤组装过程中,我们的行业已成功地自动化了先进的测试和检查过程。但是,即使在这里,我们也看不到易于对齐的自动化协议,该协议允许不同的制造商系统无缝集成。现在,我们需要自动化光纤连接。作为提供光纤装配设备的最好的制造公司的代表,我知道许多供应商也看到了这种需求。但是,没有一个制造商能够带头。这是有道理的,因为每个供应商都是其自身技术的专家,专门为流程中的特定步骤而创建。
有什么解决方案?我相信光纤行业的优质供应商必须专门团结起来,以解决这一紧迫问题。一旦我们将一个制造商协会–一个自动化工作组融合在一起,他们将需要研究其他行业如何应对这一挑战,并注意为组装设备制造商向前发展需要确定和采用的可用软件和硬件约定。这些AD Hoc选择可能会导致进一步的标准化,这只会对行业有所帮助。这是一个艰巨的任务,但是很明显现在是时候了。
问题是:我们是否可以就解决该行业问题的自动化标准达成一致?我们是否可以对自动化软件和硬件公司感兴趣,以协助我们开展这项工作?我们还能灵活地处理不同的光纤配置,连接器配置以及正在进行的技术升级吗?
光纤连接的自动化是光纤组装行业的紧迫话题。让我们开始对话,让问题向前发展。此主题必须立即解决–这是光纤组装行业必不可少的下一步。